A digital twin is an emerging technology in the PV industry. It offers vast capabilities for measuring PV plant performance and making the best engineering decisions.
The following information is based on the TRUST-PV Horizon 2020-funded research project.
What is a digital twin?
In its simplest sense, a digital twin is a digital representation of a physical object or system. A digital twin is a parametrized (2D/3D) model of a PV system that contains all the biological information needed to simulate the behavior and performance of the real PV plant it represents.
One of the primary uses of digital twins is PV performance simulation. The digital twin information can be used for the PV-performance model and simulate the performance and behavior of a PV plant it represents. This simulation can help to achieve the process of optimal decision-making.
The concept of a digital twin is to create a virtual representation of a physical system or asset, in this case, a PV (photovoltaic) plant. This digital twin contains all the necessary information to simulate the behavior and performance of the real PV plant. The key data areas required for the digital twin can be broken down into the following categories.
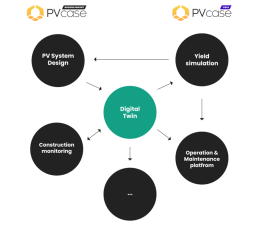
3D geospatial context
It includes the 3D representation of the PV plant’s location, considering the surrounding terrain, mountains, and other features that may cause far-shading (distant shadows) or near-shading (shadows from nearby objects like trees and buildings). It is crucial to accurately represent these shading sources to assess their impact on the plant’s performance.
Geometric properties of PV modules
The digital twin should include detailed information about the 3D geometric properties of the solar modules used in the PV plant. This consists of individual modules’ positioning, orientation, and alignment, which affects the overall energy capture.
Electrical hierarchy
The digital twin should incorporate the electrical design and hierarchy of the photovoltaic system. It involves how individual components are connected to form a functional PV system, including the arrangement of modules, inverters, and other electrical components.
Electrical properties of components
Information about the electrical properties of individual components, such as PV modules and inverters, is essential. These properties include efficiency, power ratings, electrical characteristics, and other relevant data.
To ensure that the digital twin can be effectively used throughout the PV plant’s lifecycle, it is necessary to have the following features:
– A 3D model including the PV modules, shading objects, and optical properties.
– Terrain topography information to account for variations in the ground’s elevation.
– Detailed skyline description to accurately model far shading variations within the PV plant.
– Complete electrical design and component characteristics, provided with high accuracy to avoid challenges during later stages.
– Component metadata, like serial numbers and geolocation, for unique identification and compatibility with other systems like Building Information Modeling (BIM).
– Support for changes and versioning to track modifications over time.
– A standardized and open format to allow different service providers to create compatible solutions, facilitating integration between multiple platforms.
Creating a PV plant digital twin requires specialized PV engineering software, such as PVcase Ground Mount, which can generate design files and structured information models. During the design phase of a new PV plant, it is crucial to use design software compatible with the requirements of the general PV digital twin. Advanced PV design tools help with 3D layout, topography-based design, electrical design, and other aspects, resulting in detailed and accurate PV plant 3D models.
For existing PV plants, two approaches can be used to create the digital twin:
– Comprehensive drone survey. Conducting a drone survey to scan the modules, terrain, and shading objects directly in 3D. The survey data is then post-processed and combined with PV design software to complete the digital twin. This method reduces error propagation from the documentation.
– Using existing documentation. If comprehensive drone surveys are not feasible, existing documentation can be used. It includes PV plant metadata and, if available, 2D locations, geometry of PV frames, and terrain data from a survey. Developers can also use the PVcase Ground Mount software to automate this process to a large extent.
Well-maintained documentation is crucial regarding the electrical design of an existing PV plant. Human interaction, reading, and interpreting electrical diagrams can digitize the electrical topology. PV design tools can automate the incorporation of the electrical design into the model file, including creating 3D cable paths for accurate cable length inputs. For the specifications of installed electrical components, component datasheets from the plant documentation are the primary information source.
By utilizing PV engineering software and integrating data from various sources, a comprehensive digital twin of the PV plant can be created and used for simulation, analysis, and collaboration across all lifecycle stages.
PVcase case study
Two main approaches to creating the digital twin were used in the case study conducted by our researchers. One was based on as-built documentation, and the other relied on drone survey data.
As-built documentation-based digital twin creation
In this approach, the first step is identifying and extracting the essential layers and objects from the as-built CAD design files, including terrain topography, frame polygons, DC and AC cable paths, inverters, substations, and shading objects. The terrain topography is assigned as the ground surface to adapt each deployed frame to the local ground topography. The frame polygons are then converted into PVcase Ground Mount objects, automatically adjusted to follow the terrain topography.
For the electrical design, an operator needs to read the PV plant single-line-diagrams (SLDs) or the CAD file to define the stringing pattern, assign strings to inverters, and inverters to substations using the electrical design toolbox of PVcase Ground Mount. Cabling is re-created by locating the original cable trench lines and defining them as PVcase Ground Mount trench line objects. The software’s automatic algorithms can generate DC and AC cable paths similar to the original design.
Shading objects like transformer stations and trees can be manually re-created based on the design files. Once all these steps are completed, the finalized digital twin can be visually inspected and exported in various file formats.
Drone survey data-based digital twin creation
Creating a digital twin using drone-survey data is similar to documentation-based reconstruction but with some differences. The drone survey data is delivered in a convenient CAD output format, containing ground topography, frame objects, and shading objects as mesh objects. The digital twin reconstruction using drone survey data benefits from having a 3D representation of all objects, enabling a more accurate 3D reconstruction.
However, the drone survey data only includes visible objects, so the location of cable trenches needs to be guessed. Despite this limitation, the drone survey provides a more accurate 3D representation of the PV plant. Shading objects can be accurately captured and matched with pre-defined shapes.
Yield simulation using the digital twin
Once the digital twin is created, it can be used for physics-based PV system performance simulation using software such as IMEC’s energy yield simulation framework or PVcase Yield. The report compares the simulation results of a single inverter based on the drone-based 3D model and the as-built model. The output time series of the two simulations agree well, indicating that the drone-survey-based model is accurate enough for simulation purposes.
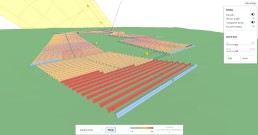
Benefits and future developments
The developed digital twin concept enables advanced, physics-based yield simulations considering the complex, 3D illumination scene and detailed electrical connectivity. The digital twin can be used throughout the entire PV plant lifecycle, from design to operation and maintenance, and can serve as a communication tool between various digital processes.
Future developments should focus on automating the discovery of electrical connectivity and component characteristics of real PV plants. Additionally, validating the accuracy of the automated digital twin-based yield simulation framework and integrating it into advanced digital services are essential next steps. Benchmarking different PV digital twins’ accuracy and efficiency at the monitoring and inspection stages could also help evaluate the value of these concepts.
Overall, the presented case study demonstrates the practical feasibility and applicability of the developed concepts and paves the way for their industrial implementation in the PV industry.
Access the full version of the digital twin white paper here.
Try PVcase tools! Schedule a demo now!
You might also be interested in:
October 10, 2024
Net energy metering: how does it work and what are the benefits?
Learn about net metering, how it works and its benefits for renewable energy users and the grid.
October 9, 2024
Solar lease vs. buy: which is better?
Explore the benefits and drawbacks of leasing or owning solar panels to determine the best option for your renewable energy needs.
October 8, 2024
Solar energy vs. fossil fuels: what’s the difference?
Want to understand the differences between solar energy and fossil fuels? Explore the pros and cons, including their environmental impacts and financial considerations.
October 7, 2024
Is solar power truly renewable or nonrenewable?
Discover whether solar energy is considered renewable or nonrenewable and explore the benefits of solar power for a sustainable future.
October 6, 2024
Understanding on-grid solar systems. Powering homes and businesses
Find out how grid-tied solar systems work, their advantages and why they're popular for homeowners and businesses looking to harness solar energy efficiently.
October 4, 2024
Solar energy vs. wind energy. Pros and cons
Discover whether solar energy is considered renewable or nonrenewable and explore the benefits of solar power for a sustainable future.
October 3, 2024
Achieving household energy independence
Discover how energy independence through solar power can benefit your household, reduce costs, and contribute to a sustainable future.
October 2, 2024
Solar powered water heaters. A comprehensive guide to their value and efficiency
Many people in rural areas have difficulty accessing financial services, a problem exacerbated by energy insecurity. Solar power can help protect rural communities from energy…
October 1, 2024
Separating solar energy facts from fiction
Explore common solar energy myths and facts. Learn the truth about the efficiency, costs, and environmental impact of solar power in this guide.
September 30, 2024
Essential solar panel maintenance for peak performance
Learn key strategies for solar panel upkeep, from regular cleaning to performance monitoring. Maximize efficiency and extend system life.
September 27, 2024
Understanding smart power grid technology
Discover how smart grids modernize power systems, enhance efficiency and integrate renewable energy sources for a sustainable future.
September 26, 2024
Why do solar panels degrade?
How and why do solar panels degrade? Explore the factors contributing to their lifespan and what measures to take to extend it.
September 25, 2024
Solar panel and battery recycling
Learn effective techniques for recycling solar panels and batteries. Discover sustainable practices, legal requirements, and the environmental impact of proper disposal methods.
September 24, 2024
Will urban air transportation become widely available?
Learn about the latest innovations and practices that can further improve the sustainability of climate-resilient crops, benefiting both farmers and the environment.
September 23, 2024
Emerging innovations in unmanned systems
Unmanned systems can perform various tasks without the hands-on operation of a human, although they’re often operated remotely. These systems are increasingly being used in…