When it comes to solar energy, modules, panels and inverters are undoubtedly important, but they alone cannot distribute electricity. Cables are one of the essential components of a solar park since they ensure the energy produced by the panels can be safely and properly transported. However, despite the growing interest in solar energy, the photovoltaic cables are a fairly recent addition to the industry. Solar cables have their own set of rules, from safety regulations to upkeep, and it’s essential to select the cable fitting for each specific project and provide suitable maintenance to ensure maximum productivity.
Basic introduction to solar cabling
Solar cables are made to be used exclusively with solar energy. By its definition, PV cable is a group of smaller wires covered by insulation. The wires can use aluminum or copper as conducting material, but commercial projects often use aluminum wires inside the cables, which is a less expensive option.
PV cables are flexible, resistant to direct sunlight or moisture, and can withstand strong heat. They are made with solar panels in mind, so usually they have the same lifespan as the rest of the equipment. One of the main elements that set PV cables apart from the regular ones is the insulation type, since regular insulation is built to last half the lifespan of the solar module, which means engineers would have to account for replacement expenses.
Engineers also need to pick a suitable cable size for the park. It should have enough length to connect various components of a PV system, as well as reflect the capacity of the PV module. Higher capacity modules or the longer distance between components would require a thicker cable in order to avoid overheating. Therefore, it’s important to consider the cabling requirements during the planning stage of the park in order to avoid re-installations or high maintenance costs.
Benefits of working with aluminum cables
Aluminum cables are lighter compared to copper ones, but the conductivity of both types remains largely the same. This makes aluminum a preferable material for larger cables since they are easier to handle.
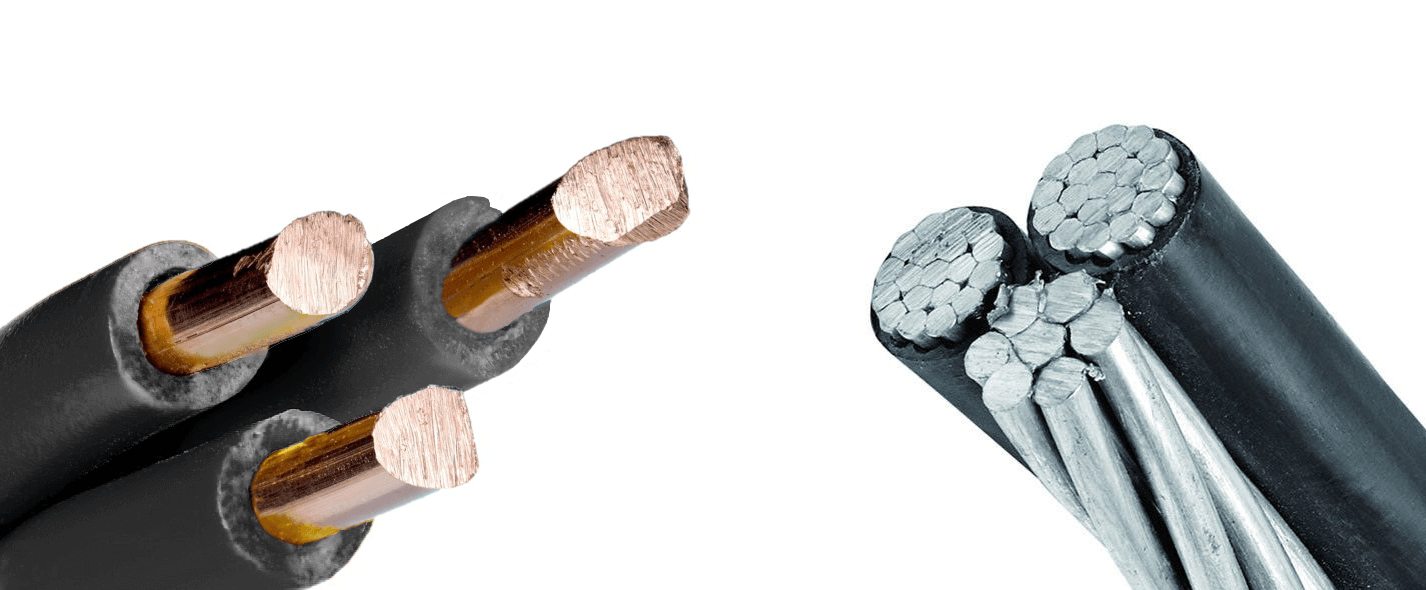
Copper cables have a slightly higher conductivity, they are more flexible yet more expensive than aluminum cables, especially in large-scope projects. The price of aluminum is lower and more stable than copper, which ensures a somewhat consistent cost of maintenance.
Aluminum cables are also relatively resistant to corrosion. Some of the drawbacks of this material are lower tensile strength compared to copper and this type of cables have larger conductors which require larger raceways. Aluminum cables also need more maintenance than copper ones, since aluminum’s expansion and contraction cycles can loosen connections over time.
What’s a BLA system?
Big Lead Assembly or BLA has a combined functionality of cable assemblies, combiner boxes, external fuses, and re-combiners. It is able to transmit power from the solar panel to the inverter disregarding some of the traditional components, such as combiner boxes and in-array trenching. BLA is part of BOS or Balance of System, which encompasses everything in a PV system aside from modules.
Despite the growing popularity of renewable energy, the construction of new solar parks remains a costly endeavor mainly due to the equipment that needs to be installed. BLA eliminates some of the O&M costs associated with solar parks, and helps manage general BOS expenses. Typical BOS systems need to run long cables across great distances and often require manual connection for its components. BLA is installed above ground, so there’s no need to create trenches for cables. It uses a plug-n-play connection feature and eliminates the need of costly specialized work. It can also be installed faster than regular BOS and requires less materials, making it less costly.
Cables in a tray vs. underground cables
A cable tray system is used to securely fasten or support cables. These systems are considered flexible and often have lower installation costs. Cable trays also help to move or add equipment with relative ease. They also keep the wires and cables neatly organized, and provide security as it ensures none of the cables are left on the ground where they are vulnerable to various damages.
In parks where using overhead construction is impractical, underground cables are suggested. They consist of one or several cores containing copper or aluminum conductors. This type of cables need to be selected according to a park’s requirements, including system voltage and current carrying capacity. Initially, underground cables can be expensive and they need to be buried, which also decreases their flexibility should any changes to the park occur. However, they are not as susceptible to damage from severe weather events and pose no danger to wildlife.
Cable maintenance
Solar parks are often built in open areas and PV cables need to withstand harsh environmental conditions. While all solar parks should follow strict regulations in order to have the longest possible life cycle, there are additional tips on solar cables which can help with the maintenance issues.
It’s advisable to use metal clips to keep the cable attached to the panel. They can keep photovoltaic cables from bending out of shape, which can cause short circuits. Using cheap or unfit materials can increase the park’s overall expenses in the long run. Cable management also includes the placement of the cables. If left loose, it’s possible that someone might trip over the cable, disrupting it or causing a shortage. The cables themselves can be buried or trenched to keep them from being damaged, but this method can get expensive should the park have the capacity to increase in size. There’s also an option to hang the PV cables, which places them in an overground formation and makes them easier to manage compared to trenching.
Preparing your cable design with PVcase
Because PV cables are an essential part of any solar park, their planning is crucial: if cables are too long or the lines are too short they become a wasteful expense. With PVcase, engineers can accurately estimate how many cables they would need to connect all the components in the park.
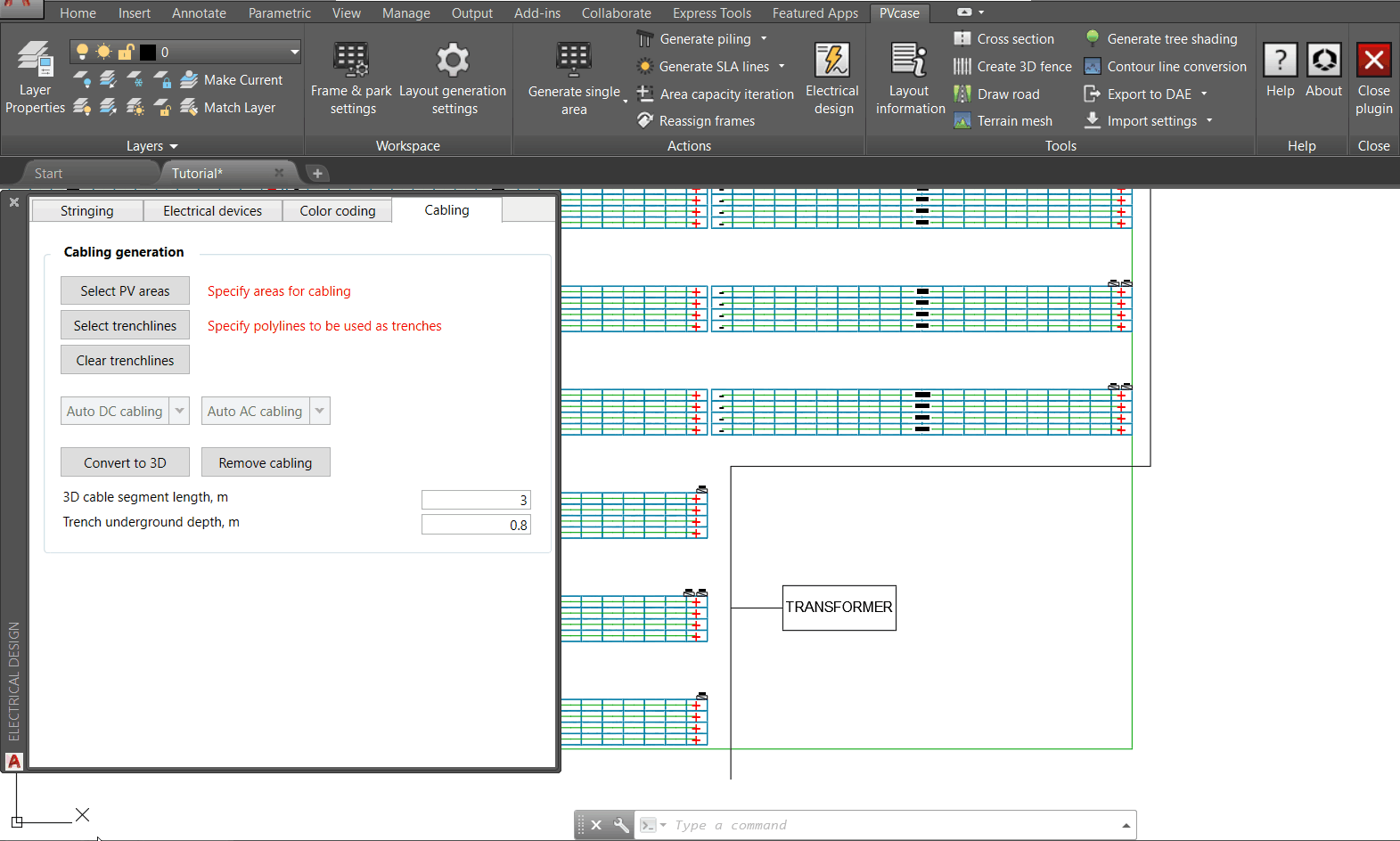
PVcase facilitates the calculation for DC and AC cabling for fixed-tilt systems, it works both with automatic cabling and semi-auto cabling. Automatic function connects all available components, while semi-auto cabling allows engineers to generate specific cabling situations. The automatic calculations function shows the best layout for the cables, taking into account the distance between components and number of viable trenches. With PVcase you can also draw manual trench lines, which can be used during the planning phase.
Request a demo today and see how PVcase can help you and your team to design your next PV system.
You might also be interested in:
July 19, 2024
Siting of PV power plants. How to adapt solar designs to complex terrains?
Choosing the wrong PV project site lowers energy output, raises costs, and risks legal issues. PVcase offers solutions. Discover them by reading the article.
July 16, 2024
Overcoming technical challenges in renewable energy projects. How PVcase transformed OHLA’s design process
Explore how OHLA overcame renewable energy design challenges with PVcase, streamlining solar park operations and achieving remarkable business growth.
July 3, 2024
Bridging the renewable energy skills gap. A success story of PVcase, Enery, and the University of Applied Sciences Upper Austria
Discover how PVcase, Enery, and the University of Applied Sciences Upper Austria have collaborated to prepare future solar engineers through an innovative educational initiative,…
July 1, 2024
Top 10 questions from Intersolar Europe 2024, answered
Get answers to the top 10 questions asked during Intersolar Europe 2024 that cover PVcase Prospect's availability, integration of PVcase products, and much more. Your question is…
June 19, 2024
Targeted solar marketing for successful landowner outreach — e-book included!
Discover how innovative strategies and Anderson Optimization's GIS Site Selection can boost solar outreach ROI and conversions. Download the ebook for more insights!
June 3, 2024
PVcase is part of the 42-month long SUPERNOVA project
PVcase, together with 19 partners from all over the world, is part of the 42-month SUPERNOVA project, focusing on O&M and grid-friendly solutions for reliable, bankable, and…
May 29, 2024
PVcase tools are now compatible with AutoCAD 2025!
We’re happy to announce that you can now use PVcase Ground Mound and Roof Mount, our flagship CAD-based tools, on AutoCAD 2025, enjoy its multiple functionalities and integrate…
May 20, 2024
PVcase is the finalist of “The smarter E AWARD” in the Photovoltaics category
We’re the finalists of “The Smarter E AWARD”! Read more about the nomination and dive into the PVcase Integrated Product Suite offering that innovates the industry.
May 14, 2024
Making great designs on good sites—the importance of topo data for PV design
Topo data is the first step in determining the success of your solar project. While the terrain is crucial in this regard, developers should also consider grid connectivity and…
April 29, 2024
How policy can shape future solar energy expansion
Policymakers and regulatory organizations must actively support solar power's growth and renewable energy advancement. Read the article to learn how.
April 25, 2024
Shading Analysis: advanced feature for C&I roof-mount solar projects is live
Shading Analysis is live! Read the article to learn about benefits, capabilities of the tool, and how it can help users and decision-makers.
April 9, 2024
PVcase wins the BNEF Pioneer Award 2024 for innovative solar design solutions
We won the prestigious 2024 BNEF Pioneers Award! Find out how our software contributes to relieving bottlenecks in the deployment of clean power.
March 29, 2024
Sustainable cities: what urban living of the future might look like
From clean energy to green bonds and renewable energy stocks, there are many ways you can invest your money in a sustainable future. Find them out by reading the article.
March 22, 2024
8 ways to invest your money in a sustainable future
From clean energy to green bonds and renewable energy stocks, there are many ways you can invest your money in a sustainable future. Find them out by reading the article.
March 21, 2024
8 business opportunities in renewable energy
There are many potentially lucrative business opportunities in renewable energy. Learn how you can use these opportunities to make money while contributing to the green…